Analysis Mesh Options
NURBS meshing parameters
Fewer polygons
More polygons
The slider controls the density of mesh faces created from NURBS surfaces.
Click to display render mesh wires on objects in viewports.
Render mesh wire preview does not display in Rendered and Raytraced display mode.
Restores the default mesh settings.
Mesh presets will not be deleted.
Switches the dialog box to the detailed meshing settings.
Detailed Mesh Options
Mesh quality presets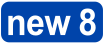
Lists the default and custom mesh settings. The presets can be accessed from different meshing dialog boxes, such as Document mesh properties, custom mesh in object properties, Mesh command, mesh file format export, and surface analysis commands.
Jagged and faster
Uses a lower density mesh to shade NURBS objects more quickly with some loss of quality.
Smooth and slower
Uses a higher density mesh to shade NURBS objects more accurately with some loss of speed.
<Custom>
Your own custom mesh settings.
Menu
Save
Save the current NURBS meshing parameters. The SubD meshing parameter is not included.
Save changes
Overwrites the selected custom preset with the current parameters.
Delete
Deletes the selected custom preset.
Export
Saves all custom presets to an xml file.
Import
Imports custom presets from an xml file.
Click to display render mesh wires on objects in viewports.
Render mesh wire preview does not display in Rendered and Raytraced display mode.
Restores the default mesh settings.
Mesh presets will not be deleted.
Switches the dialog box to the simple meshing settings.
NURBS meshing parameters
Many of these parameters are shared between the first and second steps. All steps except the fourth are run independently for each face.
Density
Density is the parameter controlled by the slider in the simple mesh controls dialog. It uses a formula to control how close the polygon edges are to the original surface. The default value is 0.5, and acceptable values are between 0 and 1. Larger values result in a mesh with a higher polygon count.
The formula is based on the size of the surface being meshed, and is used to generate a per-surface value for the Maximum distance, edge to surface parameter. This value will be smaller as the Density setting gets closer to one, and for smaller surfaces. If there is also an explicit non-zero Maximum distance, edge to surface value set in the dialog, then the mesher will use the smallest number for each surface.
In the initial grid step, this value controls the approximate maximum angle made by the surface normals at neighboring mesh vertices. Two vertices are neighbors if they are at the opposite ends of a single edge. In the mesh refinement step, quadrangles are subdivided until the angle between surface normals is smaller than this value.
This setting will influence the meshing of objects of the same shape in the same way regardless of the size of the objects. It will tend to make meshes denser in areas of high curvature and less dense in flatter areas. Setting this value to 0 disables the criterion. The default value is 0°, and the suggested range is from 5° to 90°.
This setting is scale independent.
In the initial grid step, this value controls the approximate maximum aspect ratio of the quadrangles. In the mesh trimming step, this value controls when to subdivide quads that would otherwise become too skinny when trimmed.
Smaller values result in slower meshing and a higher polygon count with more equilateral and nicely shaped polygons. Setting this value to 0 disables the criterion. The default value for this option is 0 and the suggested range, when not 0, is from √2 to 100.
This setting is scale independent.
Application
When shading long, skinny objects, use 0 for this value. This allows infinite ratios. Control the smoothness of the mesh with other parameters.
In the initial grid step, this value controls the approximate minimum edge length of the quadrangles. In the refinement step, if any edge is shorter than this value, no further division of the mesh faces occurs.
The default value for this option is 0.0001 system units and the usable range depends on the size of the model. Bigger values result in faster meshing, less accurate meshes and a lower polygon count. Setting this value to 0 disables the criterion.
This setting is scale dependent.
In the initial grid step, this value controls the approximate maximum edge length of the quadrangles. In the refinement step, quadrangles are further divided until all edges are shorter than this value.
Smaller values result in slower meshing and a higher polygon count with more equally sized polygons. Setting this value to 0 disables the criterion. The default value is 0 and the usable range depends on the size of the model.
This setting is scale dependent.
Application
Use for making sure the polygons are approximately the same size.
The distance is calculated from a mesh edge midpoint to the surface. In the initial grid step, the grid will approximately match this criterion. In the mesh refinement step, quadrangles are subdivided until the distance from a polygon edge midpoint to the surface is smaller than this value.
Smaller values result in slower meshing, more accurate meshes, and a higher polygon count. Setting this value to 0 disables the criterion. The default value is 0 and the usable range depends on the size of the model.
This setting is scale dependent.
Application
Use as a general polygon mesh tolerance setting.
The minimum number of quadrangles per surface in the initial mesh grid. Note that value applies to the shrunk untrimmed surface, so trimmed surfaces can use fewer quadrangles than this value.
Bigger values result in slower meshing, more accurate meshes and a higher polygon count with more evenly distributed polygons. Setting this value to 0 disables the criterion. The default value is 0 and the suggested range is from 0 to 10000.
This option is scale independent.
Application
Use to make sure that surfaces with very subtle details are meshed with a high enough polygon count.
If this option is true, in the mesh refinement step, Rhino uses a recursive process to refine the mesh by subdividing quadrangles until they meet the criteria defined by the Maximum angle, Minimum edge length, Maximum edge length, and Maximum distance, edge to surface options.
No refinement results in faster meshing, less accurate meshes, and lower polygon count. No refinement also means untrimmed individual surfaces and surface areas away from trim edges and joined edges are meshed with evenly sized quadrangles.
Refinement is disabled for extrusions and ruled surfaces.
If this option is true, all surfaces are meshed independently and Rhino does not stitch the mesh edges between the individual meshes of joined surfaces.
Meshes for each surface in a polysurface do not necessarily meet to form a watertight mesh. This causes faster meshing, a lower polygon count and cracks between joined surfaces in the rendered image.
If this option is false, watertight meshes are created.
Application
The Rhino mesher does not support watertight meshes made only of quadrangles unless you are meshing a single untrimmed surface. In this case, clear Refine mesh and use Jagged seams to generate quadrangle meshes.
If this option is true, all planar surfaces are meshed by meshing the surface edges and then filling the area bounded by the edges with triangles. This causes a slower meshing and a minimum polygon count on planar surfaces, especially for complex trimmed surfaces.
If this option is true, all other settings except for Jagged seams are ignored for planar surfaces, and the planar surface is meshed with as few polygons as possible.
Pack Textures
If this option is true, Rhino packs the mesh textures of the meshed polysurfaces.
How NURBS surfaces are converted to meshes?
Meshing a surface or polysurface in Rhino happens in up to four steps:
-
The first step creates a regular rectangular grid of vertices on the surface. If the surface is trimmed, the shrunk copy of the surface is used for this step. The spacing of this grid can vary along each direction, and is estimated to roughly meet the meshing criteria set in NURBS meshing parameters.
-
The second step refines the grid by subdividing some quadrangles of the initial grid until each quadrangle meets the meshing criteria. This step does nothing if “Refine mesh” is false.
-
The third step trims the mesh along the trimmed surface edges. This step does nothing if the object being meshed is a single untrimmed surface.
-
The fourth step combines coincident vertices along the joined surface edges to fill the gaps. This step does nothing if “Jagged seams” is true or if the object being meshed is not a polysurface.
All vertices generated by the meshing process are exactly on the surface. Meshing error is typically measured as the distance between the mesh edges midpoints and the surface.
In the first step, all mesh faces are quadrangles. In all further steps, new triangular faces can be introduced in the mesh. Only the second step can introduce new mesh vertices in the interior of the meshed surface. Step three and four can introduce new mesh vertices on edges.
SubD meshing parameters
Adaptive subdivision level
The adaptive subdivision level is based on the face count per SubD to avoid creating too many render mesh faces from a dense SubD. A smaller level results in faster meshing, less accurate meshes, and lower polygon count.
See Also

ExtractAnalysisMesh
Duplicate an object's analysis mesh.